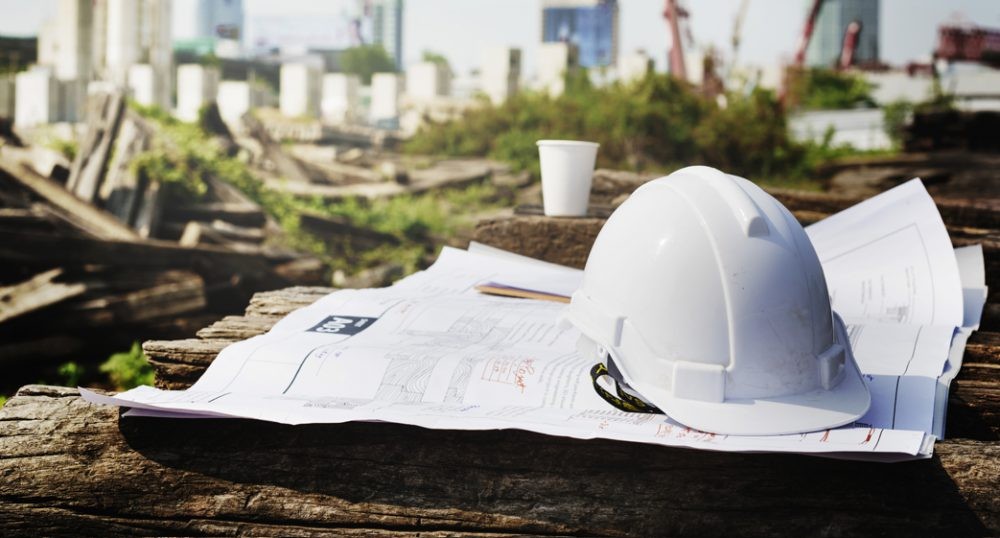
Abstract – With the variety of Delay Analysis Techniques available to schedule reviewers and analysts, it is difficult to know and implement the most reliable and effective way of demonstrating an accurate impact calculation caused by delay. Contractual requirements for time extension requests using the common term, “Time Impact Analysis”, are increasingly appearing throughout the construction industry. The broad application of the term “Time Impact Analysis” can lead to significant variances in delay calculations. Several of the AACE International’s Recommended Practices (29R-03) are commonly labeled as “Time Impact Analysis”. While each methodology may have its appropriate implementation, certain methodologies can be combined to produce a more reliable and accurate result. In the following paragraphs the Fixed Perspective Windows Delay Analysis (“Analysis”) method will be presented, which incorporates the strengths of various retrospective methods, while minimizing, if not alleviating the weaknesses. The result is an analysis that, when prepared correctly, is simple to calculate and easy to defend.
With the variety of Delay Analysis Techniques available to schedule reviewers and analysts, it can be difficult to identify and implement the most reliable and effective way of demonstrating an accurate impact calculation caused by delay in retrospect. Each analysis method has strengths and weaknesses with a series of validation requirements, so proper application of the various methods is essential to a reliable conclusion. The “Time Impact Analysis” is the method recommended within the Society of Construction Law Delay and Disruption Protocol.
In this method time impact analysis preparation includes the insertion of a delay activity into the sequence of unimpacted activities in a schedule prior to the delay event. The analyst can then determine the impact of the delay by measuring the impact to the prior completion date. Many, if not most, contract specifications that address preparation of time impact analyses are specifying a method that generally aligns with the method outlined by the Society of Construction Law. This method is virtually identical to that outlined in the AACE’s 29R-03 MIP 3.7. In addition, this methodology is similar to that which is outlined in the AACE document for prospective TIA preparations, 52R-06, with the notable exception that actual dates of the delay be used, retrospectively.
As will be detailed in the enclosed analysis, these referenced methodologies can be easily manipulated to reach biased results.
However, as construction scheduling requirements and specifications have become more stringent over the last few decades, it is possible to minimize these manipulations. More projects require monthly updates, more project staff are involved in the scheduling process, and more stakeholders provide input into the scheduling process. With increased experience and participation schedules are increasingly more consistent and accurate. Contemporaneously prepared schedule information is available more often. Delay analysis methods that rely on and incorporate this available schedule data will be consistently more reliable and accurate.
In the following paragraphs the Fixed Perspective Windows Delay Analysis (“Analysis”) method will be presented, which incorporates the strengths of certain retrospective, observational and additive methods while minimizing, if not alleviating the weaknesses. The Analysis identifies delay including mitigation and acceleration quantities, identifies concurrency, and accounts for changes in the critical path. It is equally significant to note that the Analysis will demonstrate how to select which schedule to use for the analysis to minimize manipulation. The result is an analysis that, when prepared correctly, is relatively simple to calculate and, just as importantly, easy to defend.
Common Problems with Contract Specified Delay Analyses (MIP 3.6 and MIP 3.7)
The AACE document for prospective TIA preparations, 52R-06 [2], details a recommended protocol for preparing Time Impact Analyses using a forward-looking approach. However, most project owners are hesitant to grant time extensions until the full extent of the delay is known. In shorter delays this may not be as challenging. However, on longer delay events, where the anticipated delay duration is not known, a retrospective approach is usually preferred by owners. The enclosed methodology is useful when contract documents require the actual durations of the delay and not the “forward looking” analysis detailed in 52R-06. The analysis may be prepared during the project or after, but is retrospective in time and incorporates Method Implementation Protocol (MIP) 3.7 – Retrospective, Modelled, Additive, Multi-based analysis.
The AACE document for prospective TIA preparations, 52R-06 [2], details a recommended protocol for preparing Time Impact Analyses using a forward-looking approach. However, most project owners are hesitant to grant time extensions until the full extent of the delay is known. In shorter delays this may not be as challenging. However, on longer delay events, where the anticipated delay duration is not known, a retrospective approach is usually preferred by owners. The enclosed methodology is useful when contract documents require the actual duration's of the delay and not the "forward looking" analysis detailed in 52R-06. The analysis may be prepared during the project or after, but is retrospective in time and incorporates Method Implementation Protocol (MIP) 3.7 – Retrospective, Modelled, Additive, Multi-based analysis.
As an example, a contractor may submit a Request for Information ("RFI") early in a project for installation of light fixtures that are not scheduled to be installed until very late in the project. Since the fixtures are not scheduled for installation for several months into the future, the architect may not respond immediately to the RFI. In the meantime, additional unrelated delays push the scheduled fixtures installation even further into the future. As a result, the actual duration for the response to the Request for Information extends even longer. Eventually, the architect responds to the RFI with a change. The change delays the installation of the fixtures a few days impacting the completion of the project.
In this scenario, the contractor, may choose to submit a TIA, prepared in an early schedule with the planned future duration's (blindsight) around the time of the initial RFI submission. The TIA specification states that delays should be analyzed by inserting actual delay duration's (hindsight) into a schedule just prior to the delay. Using the older schedule and the actual duration of the RFI response, the analysis would appear to demonstrate the RFI was on the critical path its entire duration, ultimately impacting the end date. By not incorporating details included in subsequent updates during the alleged delay period, the analysis misrepresents the real impact of the RFI and change.
In the following chart, Delay Event 1, representing a hindsight as-built duration of a delay activity, is inserted into a copy of a contemporaneously updated schedule. This analysis seems to demonstrate that the Delay Event 1 impacted the critical path of the project.
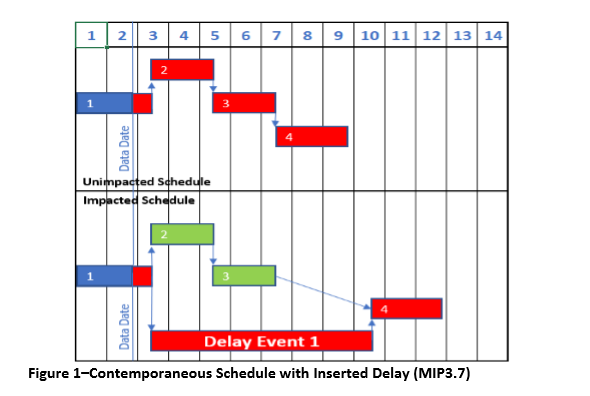
However, if the contemporaneous schedules are reviewed, the Delay Event 1 may have never been on the critical path until much later in the analysis period, once float was consumed. The following graphic illustrates a contemporaneous updated schedule with a data date in month 6 in which the Delay Event 1 is not driving the critical path. In many cases, the Delay Event 1 may not even be in the contemporaneous schedule since it is not driving an activity contemporaneously as of the data date.In this scenario, the Delay Event 1 may, or may not be a concurrent delay depending on available float and its management.

Another scenario is that the Delay Event 1 only becomes critical in a later contemporaneous update, once float is consumed. Following the completion of the Delay Event 2 impacted activities, Delay Event 1 becomes critical in the Month 10 schedule.

Using the previous examples, it is apparent that a delay analysis can be manipulated applying MIP 3.6 or 3.7 simply based on the application of terms detailed in the typical TIA specifications. This is why an Observational review of contemporaneous schedules during the delay period should be incorporated. The additive model of MIP3.7 may not include concurrent delays occurring during the delay event, or more significantly, it may not take into account changes in the critical path occurring during or prior to the delay event. In addition, TIA's are often prepared without consideration of contemporaneous updates within the delay period, which may impact the TIA's outcome. It is not uncommon for TIA's to be prepared that analyze delay events that never appear on the project’s contemporaneous updated schedule’s critical paths.
The questions remain, how can an analyst be reasonably certain when a delay impacted the critical path? How can the start of the actual delay period be reasonably identified? How can the end of the delay period be accurately be identified? How can the added or prolonged delay duration be quantified? And, how can an analysis determine if or when a particular delay was overtaken on the critical path by another delay? The following paragraphs detail an approach for preparing a single based or multi-based TIA (MIP 3.6 or 3.7), where each of these considerations are addressed and, as a result, the TIA is more reliable and more importantly, defendable. In summary, the Analysis addresses and corrects the common TIA specification approach of inserting delay events into a schedule prior to the delay event. “Prior to the delay event” is often manipulated and, based in the arguments below, should be adjusted to state, “Prior to the when the delay event became critical”.
How the Fixed Perspective Window Analysis Method fits into the AACE International’s RP for Forensic Scheduling
As stated in the previous section, the Analysis is a two-stepped process for analyzing delays that incorporates sections of the AACE International’s 29R-03 Recommended Practices. The Analysis is a retrospective approach that incorporates both the observational and modeled approach.
The first step includes the exercise of reviewing a Progress Period Window Looking Forward and Backward as part of the Observational model, Dynamic Logic Observation, and more specifically the Contemporaneous / As-Is and/or Contemporaneous / Split, MIP 3.3 or 3.4 [1]. This approach provides the analyst with an opportunity to review the project’s critical path, as memorialized during the project, before and after the delay event, and as documented in the submitted schedule updates. It is an accurate quantification of the delay event from start to finish, including the time frame of when the delay event became critical and when it was finished or when another event took over the critical path.
The analysis requires the project baseline schedule and periodic schedule updates that were prepared contemporaneously during the project, and whose network logic may differ to varying degrees from the baseline and from update to update [1]. It can be implemented using all periods or grouped periods as long as each individual period is reviewed to ensure a comprehensive analysis and to avoid utilization of subjectively selected data.
The second step in the Analysis incorporates the findings of the first step into the Modeled approach, specifically the Additive Modeling with the Single Base or Multi-Base, as defined in MIP 3.6 or 3.7, or the "TIA", in order to meet the common contractual requirements for measuring project delays.
Prerequisites for Preparation of the Fixed Perspective Windows Analysis
Prior to preparation of the Analysis a thorough review of the baseline and monthly updated schedules should be performed with sufficient and appropriate Source Validation Protocols as detailed in the AACE 29R-03 SVP 2.1 – 2.4. Although the AACE RP for Forensic Scheduling states that "Forensic Scheduling is a technical field associated with, but distinct from, planning and scheduling field", experience with planning and schedule is essential in order to avoid misapplication of the enclosed analysis. The analyzer “is assumed to have advanced, hands-on knowledge of all components of CPM analysis and a working experience in a contract claims environment involving delay issues”[1]. A hands on, in-the-field scheduling experience is also valuable.
Performing a Fixed Perspective Windows Analysis – Part 1
The Fixed Perspective Window Analysis in the enclosed Analysis is a detailed and multi-view analysis of a period, or window, of project time using the contemporaneous time frame schedule updates prepared during the course of the project. The analysis is multi-view in that it reviews the fixed window of time from two perspectives, before and after the window of time. The term fixed perspective addresses a common generalization about the windows analysis method where analysts define their own time periods, often subjectively and materially affecting the end results. The analysis is prepared one window at a time. It assumes the periodic schedule updates are reasonably accurate, and the Source Validation Protocols for baseline schedules and updates have been reviewed.
The Analysis is a two-step approach to preparing the traditional TIA that ensures an accurate and reliable result when calculating delay events. It incorporates the fixed approach of reviewing the contemporaneously prepared schedule updates without modification (MIP 3.3) and incorporating the results of that review into an additive model (MIP 3.7), required in a common TIA contract specification. The review requires that each of the Critical Path Method (CPM) schedules, prepared during the project, be used. The critical path activities are the primary activities analyzed with their associated changes and impacts.
The goal of the Analysis is to isolate only those delays that impacted the critical path and ultimately the completion of the project. Therefore, the Analysis does not attempt to analyze every delay event, but only the critical path delay events as they impacted completion once construction began. The Analysis includes both an as-built critical path analysis to accurately identify and analyze any changes or delays to the critical path, and project completion included in the submitted schedules (MIP3.3). It also includes a contemporaneous analysis of delays (MIP3.7) whereby the delay issues are inserted into the schedule update nearest to the actual start of the delay issues, in order to meet a TIA contract requirement. The methodology includes a detailed review of each project schedule update prepared during the project, analyzing the specific periods between the schedule updates as “progress period windows”. The review includes: 1) a review of the progress period window looking forward, using the schedule update prior to the progress period window; and 2) a review of the progress period window looking backward, using the schedule update at the end of the progress period window. This is illustrated in Figure 4.

The first step in preparing the Analysis incorporates a review of specific “windows” of time looking forward using a static model of the contemporary updates, an implementation of AACE International’s 29R-03, MIP 3.3. The Fixed Perspective Window Analysis Looking Forward includes a detailed analysis of each progress period (periods in between monthly updates), or a window analysis. First, the analyst should perform a detailed review of the critical path in the monthly update prior to the progress period window. Second, a progress verification is performed comparing the planned critical path activities to actual performance included in the subsequent updated schedule. Third, the monthly update critical path is compared to actualized performance in the subsequent update to verify whether the critical path had changed during the reported period. Finally, changes in sequence and/or duration's are reviewed to determine if the critical path changed during the period.In addition, changes in future planned activities are evaluated to determine schedule impacts, gains, or losses outside of the selected evaluation period in order to demonstrate how overall changes impacted the final completion date.
In addition to delay impacts, the Analysis identifies and quantifies efforts made through re-sequencing work activities, or reduced duration's that may have recovered time during the project, incorporating MIP 3.4[1]. The following paragraphs include a review of two windows from a sample project to demonstrate delay calculation using the Fixed Perspective Window Analysis.
The Forward-Looking Window Analysis for Period 1
Figure 5 includes a bar chart from a contemporaneous schedule (Schedule 1) compared to a subsequent schedule update with a data date one month later (Schedule 2). The Forward-Looking comparison is comparing changes that occurred to the critical path in the subsequent updated schedule. The spreadsheet area of the bar chart schedule includes three columns: the activity name, variance in start dates, and variance of finish dates. The comparison bars for Schedule 2 are shown below the Schedule 1 bars. The color of the bars indicates whether the activities are critical or not in both schedules. As an example, the top bars for the Phase 1 activities are red indicating that they are critical in the current schedule, while the comparison bars are black, indicating that, in the subsequent schedule, the activities are no longer critical. The first three activities in the “Phase 2” section were not critical, but in the subsequent schedule these activities have become part of the critical path. Notations are numbered and include in a Table 1 after the bar chart.

The following comments in Table 1 detail notations from Figure 5.

The Backward-Looking Window Analysis for Period 1
Figure 6 includes a bar chart from the contemporaneous schedule (Schedule 2) compared to a previous schedule update with a data date one month earlier (Schedule 1). This perspective is reviewing the same time frame as Figure 5, except comparing changes that occurred to the critical path in the previous updated schedule. The spreadsheet area of the bar chart schedule includes the same three columns: the activity name, variance in start dates, and variance of finish dates. The comparison bars for Schedule 1 (previous update) are shown below the Schedule 2 bars (subsequent update). Once again, the color of the bars indicates whether the activities are critical or not in both schedules.
As an example, the top bars for the Phase 1 activities are not red indicating that they are no longer critical in the current schedule, while the comparison bars are red, indicating that, in the previous schedule, the activities were critical. The first three activities in the “Phase 2” section were not critical, but in the subsequent schedule these activities have become part of the critical path. In this window of time between Schedule 1 and Schedule 2 the notations are identical and are detailed in the previous Table 1.

A summary of the events in the first window are detailed in Table 2. In summary, the delay event impacted the critical path 18 days. Considering the gain in production of the previous critical activity of 1 day, the net result to the schedule is a 17-day loss.

The Forward-Looking Window Analysis for Period 2
Period 2 is the subsequent month from the month analyzed in Period 1. Figure 7 includes a bar chart from the contemporaneous schedule (Schedule 2) compared to the subsequent schedule update with a data date one month later (Schedule 3). The Forward-Looking comparison is comparing changes that occurred to the critical path in the subsequent updated schedule. The spreadsheet area of the bar chart schedule includes the same three columns as the previous bar charts: the activity name, variance in start dates, and variance of finish dates. The comparison bars for Schedule 3 are shown below the Schedule 2 bars. The color of the bars indicates whether the activities are critical or not in both schedules.
As an example, the top bars for the Phase 2 activities are red indicating that they are critical in the current schedule, while the comparison bars are black, indicating that, in the subsequent schedule, the activities are no longer critical.
There is a gap between the activities, “Exc/Grade Detours” and “Pave Detours”. This is indicative of added activities in the subsequent schedule (or extended duration's if a filter is being used) causing a change in the critical path.
Notations are numbered and included in Table 3 following the bar chart.

The following comments in Table 3 detail notations from Figure 7. Identification of recovery/acceleration in the schedule comparisons coincide with the MIP 3.4 criteria.

The Backward-Looking Window Analysis for Period 2
Figure 8 includes a bar chart from the contemporaneous schedule (Schedule 3) compared to a previous schedule update with a data date one month earlier (Schedule 2). This perspective is reviewing the same time frame as Figure 7. The spreadsheet area of the bar chart schedule includes the same three columns: the activity name, variance in start dates, and variance of finish dates. The comparison bars for Schedule 2 (previous update) are shown below the Schedule 3 bars (subsequent update). Once again, the color of the bars indicates whether the activities are critical or not in both schedules. As an example, the top bars for the Phase 2 activities are not red, indicating that they are no longer critical in the current schedule. While the comparison bars are red, indicating that, in the previous schedule, the activities were critical. The first two activities in the “Phase 2” section were critical, but in the subsequent schedule these activities were no longer on the critical path. Notations from Figure 8 are included in Table 4. The comments are similar to the Forward-Looking comparison with added information from the later schedule, unavailable in the forward-looking schedule.


A summary of the events in the second window of time are detailed in Table 5 below. In summary, the Delay Event 1 impacted the critical path an additional 19 days. Another Delay Event (Delay Event 2 – Paving Mix Design Resolution), impacted the critical path an additional 10 days this period. Subsequent re-sequencing reduced the impacts by 10 day for a net loss of 19 days this period. With the 18 days lost in the previous period the net loss by Delay Event 1 is 36 days.

NOTE: There are two issues not in these conclusions: 1) Delay Event 2 overtook Delay Event 1 on the critical path 10 days prior to its planned completion date in Schedule 3. No conclusions were drawn regarding any of the overlap period that may have been a concurrent delay. 2) The gain resulting from resequencing may be contributed to either delay depending upon which party initiated the recovery/acceleration efforts.
Performing a Fixed Perspective Windows Analysis – Part 2
.Part 2 of the Analysis complies with the 29R-03 MIP 3.7 and 52R-06 Time Impact Analysis, if the reviewer is requiring a known completion of the delay period (retrospective). Part 1 identified the duration of the delay events and when the various delay events impacted the critical path. With this information, separate and often overlapping delays can be inserted into the appropriate schedule prior to the start of the delay’s impact to the critical path. In the above example Delay Event 1 impacted the critical path in Schedule 2. Therefore, the appropriate schedule in which to insert a delay activity representing Delay Event 1 (37 days) is in Schedule 1. Delay Event 2 impacted the critical path in Schedule 3. Therefore, the appropriate schedule for the MIP 3.7 analysis of Delay Event 2 is in Schedule 2.
The Advantages of the Fixed Perspective Window Analysis
The previous Analysis meets all of the Underlying Fundamentals and General Principals laid out in the AACE Recommended Practices for Forensic Scheduling,: 1) It uses CPM Calculations; 2) The concept of Data Date is an integral part of the Analysis; 3) network float is identified and accounted for; 4) Float is based on the appropriate schedule; 5) Sub-Network Float can also be evaluated when needed; 6) the calculation of impacts can be demonstrated in relation to the critical path; and, 7) all available schedules are considered. Preparing an analysis as described herein, where Impacts of potential causes of delay are evaluated within the context of the schedules in effect at the time when the impact or multiple impacts happen, increases the accuracy in quantification. In addition, the fixed time periods provide the best as-built of not only project dates and sequences, but an as-built view of the prospective critical path as contemporaneously prepared.
Conclusion
Guidelines for preparation of Time Impact Analyses prescribed in many contract specifications align with the MIP 3.7 methodology. The guidelines can be vague and easily manipulated. Therefore, a proper application of a Time Impact Analysis methodology is essential to reach a reliable conclusion. The enclosed method for measuring delays incorporates the strengths and minimizes the weaknesses of common delay analyses by combining an application of MIP 3.3 to MIP 3.7. The combination, as described in the previous paragraphs, will minimize errors and manipulations by identifying the appropriate schedule to use as a basis for the Time Impact Analysis and a reliable duration of the analyzed delay, while meeting the typical contract requirement for preparing a TIA.