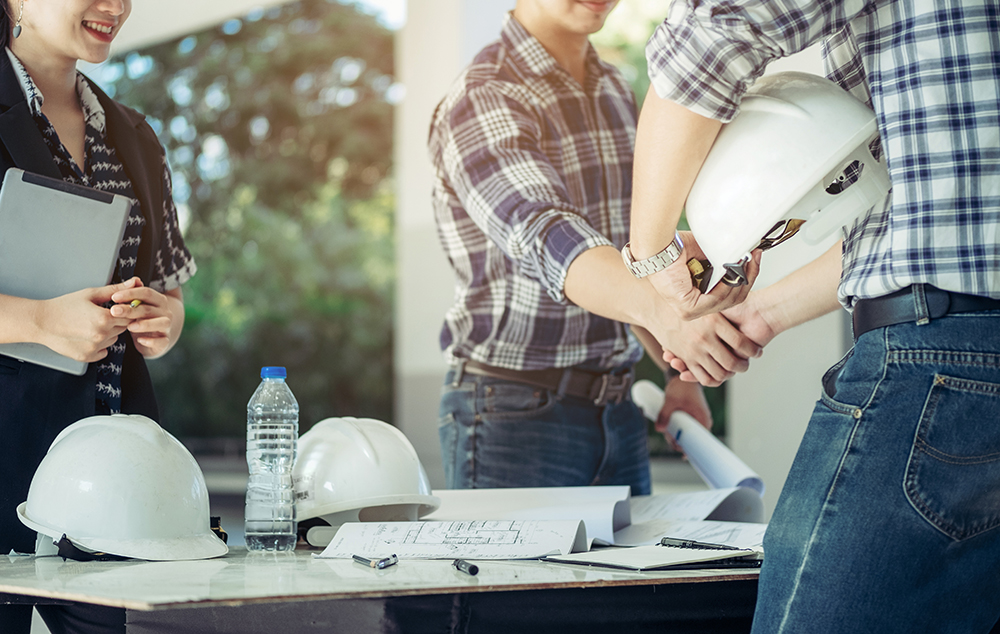
So much is written and discussed these days to help teams execute organizational objectives. It is not enough to have thorough knowledge of a particular strategy, and good intentions will not get the job done. What organizations need is a culture or environment that fosters execution, or follow-through on goals or strategies communicated from the top. While many construction executives focus sincere effort on high-level strategies and goals, there is often a breakdown at the implementation level. No program strategy will be successful without the team and tools in place at the project level to execute that strategy.
Program strategies can vary as much as the number of programs that exists; from individual construction project execution to enterprise software implementation, from a rollout of corporate standards, to a management accountability program. Successful execution of the program strategy, no matter what it is, will generally consist of three themes that must flow down from the executive level.
Empower the Team
The successful project execution process begins with a systematic project team approach to planning the rollout of the strategy. Without a rigorous dialogue on the detailed day to day strategy of an entire project among those assigned to accomplish it, it is impossible to move forward as a coherent team. With the dialogue up front before the project even begins, the team becomes more of a unit and their effectiveness reaches way beyond their individual skill or knowledge base.
This principal is demonstrated regularly in sports. Every player on a football team, no matter what position they play is a part of game-plan discussions. It is important that each player sees how their efforts fit into the big picture. The quarterback may participate at a different level in the discussion, but if an offensive lineman is unaware of his part in the overall plan, the quarterback may have a rough game.
It is no different for a construction project, or group of projects. The most effective game-plan sessions are those that include participants from the entire project management team. These sessions allow the team to discuss in detail the “how’s” and “what’s” of the project and form a cohesive plan for project execution.
As a professional planner and scheduler I have participated, as a facilitator, in a wide variety of these types of “game-plan” sessions, usually lasting one or two days at the beginning of the project. The focus and team spirit that comes from these meetings always benefits the execution mentality and helps link organizational strategy to field operations.
Establish Milestones
Milestones help execution teams (Project Management Teams) establish goals and work together as a team to accomplish them. Milestones also help the executive know if a project is in trouble before it is too late. Some effective guidelines for milestone setting are:
- Establish some milestones early in the project. Unlike a sporting event with a real-time scoreboard most projects/programs are moving forward in the dark when it comes to measuring their score on time and budget. So, an executive will need to set up a scoreboard with milestones if he wants to know how his team is doing.
- Establish rewards for milestone accomplishment. By spreading rewards or bonuses over the course of the project for specific accomplishments an executive benefits from the ongoing accountability of the project team. The execution team benefits from the ongoing team motivation and accountability offered by the milestone rewards.
Ask the Right Questions
It is so important for executives to know the right questions to ask and to know when to ask them. Most of the construction claims that I have been involved with over the years could have been avoided had executives (those with experience and vision) understood this simple process.
To ask the right questions an executive must be involved. In the “game-plan”, or planning and scheduling sessions mentioned above, an executive can learn so much about the team he is depending on to execute. Those sessions open up so many opportunities to ask “How are you going to do that?” or “What resources will that require?” Asking the right questions forces the team to think about their assumptions and contingencies. Asking the right questions also exposes strengths and weaknesses among the team members. So often weaknesses are not discovered until it is too late when execution hopes become replaced by recovery necessities.
Secondly, to ask the right questions the executive must be informed. Having the right information allows the executive to understand the proper management questions. I’ve known executives who would meet with their project managers and maintain a cordial relationship with general conversation about the project and major issues. Their intent may have been to keep the project manager motivated and keep the project moving forward. Their intent may have been to become more informed on the status of the project. In either case, without the proper information to know what questions to ask these executives were so often left holding the bag.
Clear and succinct reports that compare current status with planned status, milestone status, progress on the critical path, along with budget and projections provide the information needed to ask the right questions. When the right questions are asked the execution team will stay motivated because problems are always in the open. Executives stay better informed and their experience brings earlier and more effective resolution to project issues.
John Jackson is a professional scheduler, expert claims consultant, and enterprise software implementation and corporate standards specialist. For question please contact jjackson@encrp.com.